Thermal Management Solutions for Long Term Protection of Military and Aerospace Electronics
Electronics for military applications are expected to operate first-time, every time in some of the most hostile and demanding environments. Military programmes are often designed to run over several decades, with hardware likely to be updated several times over the programme's duration. Similarly, most aerospace electronics will be compromised by harsh operating environments; significant amounts of vibration, often extreme variations in operating temperature, as well as the risks of exposure to chemicals, de-icing fluids and the like, will all take their toll unless adequately protected. Commercial and military aerospace applications, too, will typically have multi-decade programme lifetimes and the hardware will usually be upgraded several times during its service life. Long term protection of military and aerospace electronics is thus important.
Electrolube is an ISO 14001 accredited, UK based company that has been manufacturing high-specification, formulated chemical products for electronics manufacturers since 1941. Serving a plethora of industries including the aerospace, military, marine, automotive and telecoms industries, Electrolube provides both bespoke and ‘off-the-shelf’ products, including thermal management formulations, conformal coatings, encapsulation resins, contact lubricants and aqueous and solvent-based cleaning materials, as well as more general maintenance and service aids.
Electrolube has extensive experience of working within these sectors, its relevant systems and product formulations being fully compliant with industry standards, including MIL-STD 810 (environmental) and MIL- 1-46058-C, now superseded by IPC-CC-830B, IEC-61086 and UL746 (conformal coating).
Electrolube’s primary and secondary conformal coating protection systems, include products based on acrylic, urethane, silicone, epoxy and parylene formulations, offering features that give enhanced protection against certain specified environmental conditions (high humidity, condensation risk, high operating temperatures, etc.), which meet appropriate standards such as US MIL-1-46058C, UL746, British Ministry of Defence DEF-STAN 59/47 Issue 4 and UL746CQMJU2.
However, it's not just about extending the lifetime of electronic systems in storage or in duty, but addressing all concerns regarding their reliability and performance; thermal management is key to achieving this. The development of aerospace and defence electronic systems is driving significant increases in power densities, with the result that thermal management has become a significant challenge for suppliers of hardware to this sector.
Electrolube can provide a particularly versatile range of products that address these thermal management issues, providing effective heat dissipation and preventing device failure as a result of elevated operational temperatures. Most electrical components are low powered devices that produce negligible amounts of thermal energy; however, there are also many devices – such as CPUs, power diodes, power transistors and so on – that produce significant amounts of heat and it is important that this heat is removed from the device quickly and efficiently to ensure optimal performance, and to prevent premature component failure. This is somewhat exacerbated by the trend for product miniaturisation and the use of compact, higher powered devices, which place greater demands on thermal management systems.
Heatsinks are commonly deployed to conduct and radiate heat from high power electronic components, the device and heatsink - usually solid substrates - being mechanically bolted together. Ideally, the surfaces of these substrates should be perfectly smooth, but this is not always possible and, as a result, air gaps will be present at the interface. Air is an extremely poor thermal conductor (0.024W/mK), and so the interface between the heat-sink and device will compromise heat transfer efficiency.
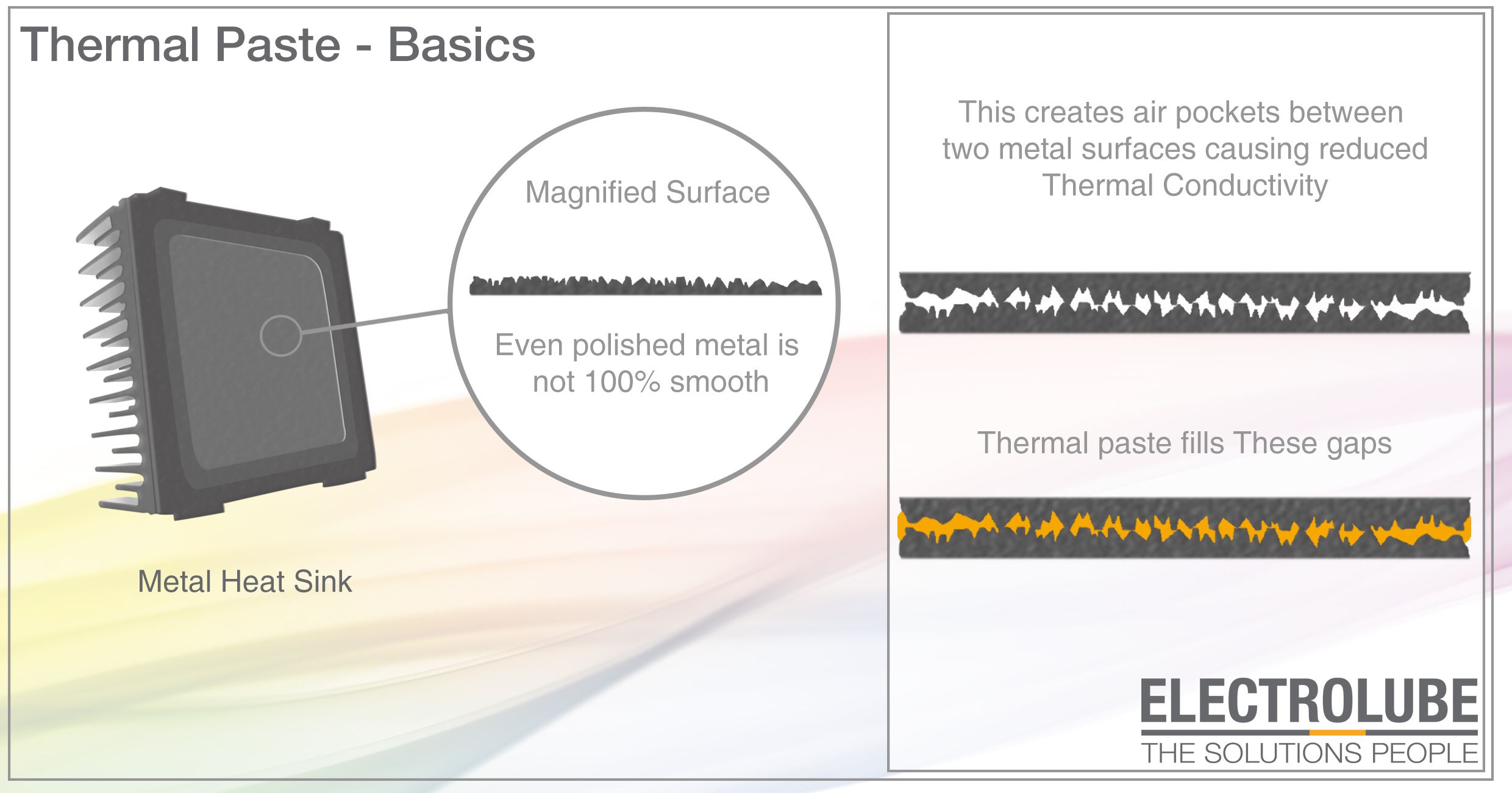